USB2.0 and USB3.0 interface PCB layout requirements
USB is the acronym for Universal Serial Bus, a serial bus standard for connecting external devices, but also a technical specification for input/output interfaces, widely used in personal computers and mobile devices and other information communication products, and extended to photographic equipment, digital TV (set-top box), game consoles and other related fields.USB2.0 interface has a transmission rate of up to 480Mbps, USB3.0 maximum transmission bandwidth of up to 5Gbps, USB3.0 introduction of full-duplex data transmission, USB layout and wiring has its corresponding design requirements.
USB2.0 and USB3.0 interface pin definition shown in Figure 1.
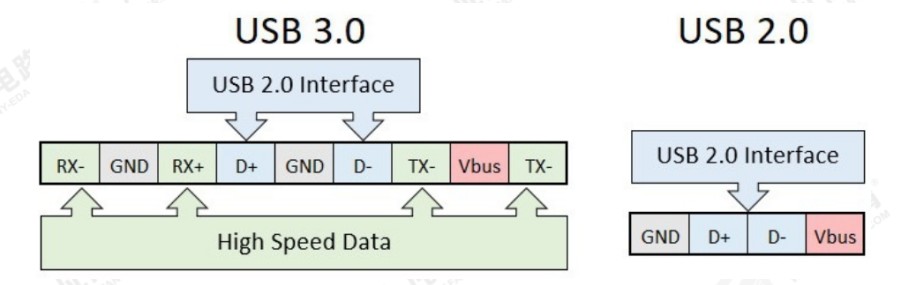
Figure 1 USB 2.0 and USB 3.0 pin definition
First, the USB interface PCB layout requirements
1, USB should be close to the interface board edge or structural positioning placed, out of the board edge of a certain position (except for direct insertion), easy to plug and unplug;
2, ESD, common mode inductors near the USB interface, placed in the order of ESD-common-mode inductors-resistive capacitors;
3, pay attention to the distance between the ESD and USB, leaving a certain distance, consider the case of post-soldering.
4, in the layout, try to make the shortest differential line to shorten the differential line distance.
Second, the USB interface PCB wiring requirements
1, USB to go differential, impedance control for 90 ohms, and packet processing, the total length of the best not to exceed 1800mil.
2, as far as possible to shorten the length of the alignment, give priority to high-speed USB differential (RX, TX differential) wiring, USB differential alignment in the alignment, as far as possible to reduce the layer of holes, so that you can do a better job of impedance control, to avoid the reflection of the signal;
3, the over-hole will cause discontinuity in line impedance, in each punched hole for layer change the place to add a pair of reflux ground over-hole, for signal reflux layer change.
4, if the USB positioning columns on both sides of the connection is a protective ground, split to ensure that the distance from the GND is 2MM, and more holes in the protective ground area to ensure full connectivity, as shown in Figure 2.
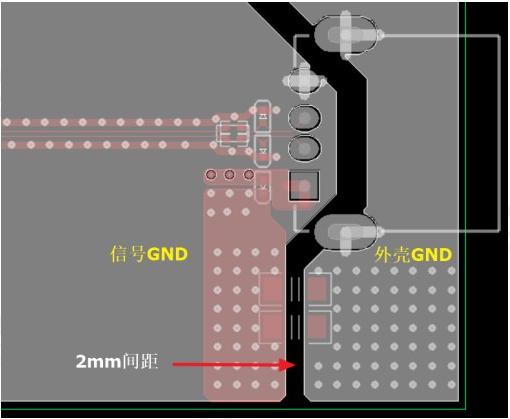
Figure 2 shell GND and signal GND isolation
5, due to the distribution of pins, holes, and alignment space and other factors exist to make the differential line length is easy to mismatch, wiring length once the mismatch, the timing will be deviated, but also cause common mode interference, reducing signal quality. Therefore, the corresponding differential pair mismatch to make compensation, so that the length of the line to match, the length difference is usually controlled within 5 mil, compensation in accordance with the differential isometric specification to carry out.
USB2.0 and 3.0 PCB wiring requirements compared to the following Table 1 shows:
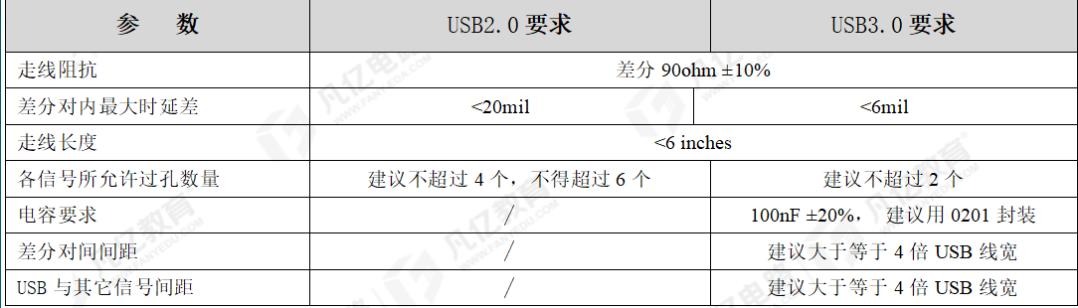
Table 1 USB2.0 and USB 3.0 PCB wiring requirements
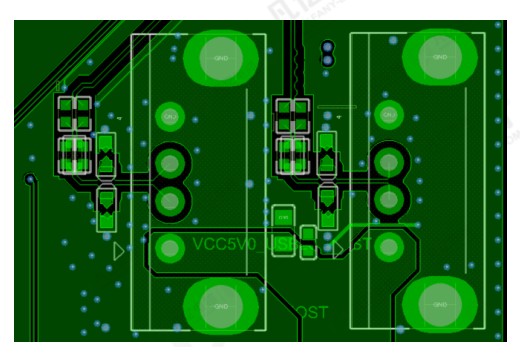
Figure 3 Layout and wiring for USB 2.0
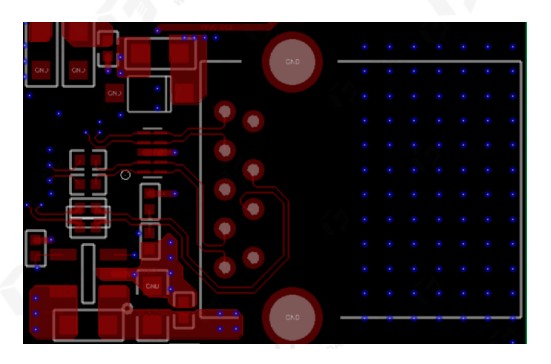
Figure 4 USB 3.0 layout and wiring
Third, Type C interface PCB design
USB Type C, also known as USB-C. It should be noted that Type-C is only an interface, and the version of USB does not have any relationship. The highlights of the interface is a slimmer design, faster transmission speeds (up to 10Gbps and more powerful power transmission (up to 100W). type-C double-sided plug interface is the most important feature of the support for USB interfaces inserted on both sides, mainly for the thinner, lighter, slimmer devices. The pinout of the Type-C interface is shown in Figure 7-23 below.
Figure 7-23 Pin definitions for the Type C interface
PCB design requirements for Type C interface:
1, ESD, common mode inductors close to the Type C interface, placed in the order of ESD → common mode inductance → resistive capacitance; the same should also pay attention to the distance between ESD and Type C, leaving a certain distance, consider the case of post-soldering.
2, TX signal line coupling capacitance should be placed close to the interface, RX signal line coupling capacitance provided by the device side, as shown in Figure 7-24;
Figure 7-24 TX signal line coupling capacitance
2, Type C differential alignment impedance control 90ohm ± 10%, in order to ensure the continuity of the impedance, there should be a good reference plane and not across the split, the number of signal punching for layer change is not more than 2.
3, Type-C has RX/TX1-2 four groups of differential signals, two groups of D + / D - differential signals, a total of six pairs of differential lines, differential signal lines require at least adjacent to a ground plane, both sides are adjacent to the ground plane is best, the alignment is as short as possible, the longest alignment should not exceed 6inchs.
4, to ensure that the Type C differential line length matching, internal isometric error <6mil, isometric in accordance with the differential isometric specification.
5, to ensure that Type C differential for inter-pair or differential for other signals, intra-pair spacing is recommended to be greater than or equal to 4 times the Type C line width. With other signals between the spacing to maintain as much as possible is greater than or equal to 4 times the Type C line width;
6, CC1/CC2 are two key pins, the role of many: detection of connections, distinguish between positive and negative, distinguish between DFP and UFP, that is, the master-slave configuration Vbus, the alignment of the face to be thickened to deal with.
Note: Type-C connector operating rate ≥ 8Gbps, please follow the connector optimisation recommendations in Chapter 5, Section 5.6 for design processing!
Figure 7-25 Type-C Connector Wiring Schematic