What is PCB and what are the considerations in the PCB processing?
[Read More] To improve your understanding of PCB, this article will introduce the basic situation of PCB, as well as the considerations in the success of PCB processing.PCBs have many functions in electronic devices, such as providing certain electrical functions. In order to improve your knowledge of PCBs, this article will introduce the basic information about PCBs, as well as the considerations for successful PCB processing. If you are interested in the PCB or the contents of this article, you may wish to come with me to continue reading down Oh.
First, PCB
PCB (printed circuit board) that printed circuit board, referred to as the printed circuit board, is one of the important components of the electronics industry. Almost every electronic device, from small to electronic watches, calculators, large to computers, communications electronics, military weapons systems, as long as there are integrated circuits and other electronic components, in order to make the electrical interconnection between the various components, are to use the printed circuit board. The printed circuit board consists of an insulating base board, connecting wires and pads for assembling and welding electronic components, with a dual role of conductive lines and insulating base boards. It can replace the complex wiring to achieve the electrical connection between the components in the circuit, not only simplifies the assembly of electronic products, welding work, reduce the traditional way of wiring workload, greatly reducing the labour intensity of workers; and reduce the size of the machine, reduce product costs, improve the quality and reliability of electronic equipment. Printed circuit board has good product consistency, it can be standardized design, conducive to the production process to achieve mechanization and automation. At the same time, the whole piece of printed wiring board after assembly and commissioning can be used as an independent spare part, which facilitates the interchangeability and maintenance of the whole product. At present, printed wiring boards have been extremely widely used in the manufacture of electronic products.
The first printed circuit boards used were paper-based copper-clad printed circuit boards. Since the emergence of semiconductor transistors in the 1950s, the demand for printed circuit boards has risen sharply. In particular, the rapid development and widespread use of integrated circuits, so that the size of electronic equipment is becoming smaller and smaller, circuit wiring density and increasing difficulty, which requires the printed board to be updated. At present, the varieties of printed boards have been developed from a single panel to double-sided, multi-layer board and flexible board; structure and quality has also been developed to ultra-high density, miniaturization and high reliability degree; new design methods, design supplies and board materials, board technology continue to emerge. In recent years, a variety of computer-aided design (CAD) printed circuit board applications have been popularized and promoted in the industry, in the specialized printed circuit board manufacturers, mechanization, automated production has completely replaced the manual operation.
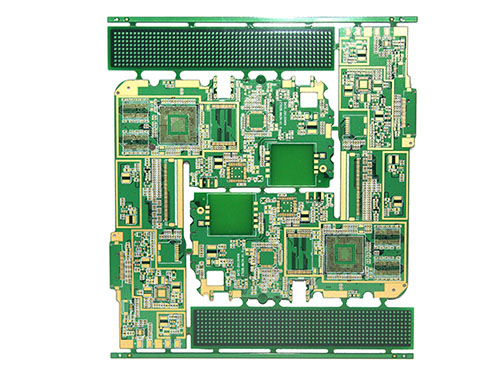
1) PCB before cutting
Laminate cutting before the PCB baking (150 ℃, time 8 ± 2 hours) is to remove the moisture in the board, while making the board in the resin completely cured to further eliminate the residual stack in the circuit board, which is useful for preventing the board warpage.
Currently, many double-sided and multilayer boards still insist on a baking step either before or after lay-up. However, there are exceptions in some board factories. Drying times in PCB factories are also currently inconsistent, ranging from 4-10 hours. It is recommended that this is determined by the grade of printed board produced and the warpage requirements of the customer.
Bake the whole piece and then cut into a jigsaw or undercut and then bake, both methods are possible. It is recommended that the board is baked after cutting and the inner board should also be baked.
2) Warping of prepreg
After laminating the prepreg, the warp and weft shrinkage rates are different, so it is important to differentiate between warp and weft when dropping and laminating, otherwise it will easily cause the finished board to warp after laminating, which is difficult to correct even if pressure is applied to the baked board.
Many of the reasons for warping of multi-layer boards are due to the lack of distinction between the warp and weft directions of the prepreg material when laminating, and the random stacking.
How do you differentiate between warp and weft? Rolled prepreg is rolled in the warp direction and the width direction is the weft direction; for copper foil sheets, the long side is the weft direction and the short side is the warp direction. If you are not sure, you can check with the manufacturer or supplier.
3) Stack relief after lamination
After hot and cold stack the multilayer board is removed, cut or milled off the burrs and then placed flat in a 150°C oven for 4 hours to gradually release the stresses within the board and allow the resin to fully cure, this step cannot be omitted.
4) Thin plates need straightening when plating
When 0.4 to 0.6mm ultra-thin multilayer boards are used for surface plating and pattern plating, special pinch rollers should be made. After clamping the thin plate on the automatic plating line on the clamping roller, clamp the entire clamping roller with a round bar. String the rollers together and straighten all the sheets on the rollers so that the plated sheets are not distorted.
Without this measure, after plating with a 20 to 30um copper layer, the sheet will bend and be difficult to remedy.
5) Cooling of the board after hot air levelling
PCBs levelled with hot air are subjected to high temperatures (approx. 250°C) from the solder bath. After removal they should be placed on a flat marble or steel plate to cool naturally and then sent to a post-processor for cleaning, which helps to prevent the board from warping.
In some factories, in order to improve the brightness of the lead-tin surface, the board is placed in cold water immediately after hot air levelling and removed for post-processing after a few seconds. This hot and cold shock can cause warping of certain types of boards. twisting, delamination or blistering.
Alternatively, an air float bed can be fitted to the equipment for cooling.