FR-4 sheet process
The generation process of FR-4 sheet material usually includes the following steps:1. Raw material preparation: Prepare raw materials such as glass fiber cloth and epoxy resin, and cut the glass fiber cloth into the required size.
2. Sheet pretreatment: Soak the glass fiber cloth in epoxy resin to make it fully impregnated. Then, after heating treatment under high temperature and high pressure, the resin is cured and closely combined with the fiber cloth. This process is called curing.
3. Copper foil layer treatment: Cover the surface of the cured sheet with copper foil and perform treatments such as etching to form the required circuit pattern.
4. Subsequent processing such as drilling and cutting: Perform subsequent processing such as drilling, cutting, and grinding on the sheet according to actual needs to meet different application requirements.
5. Quality inspection: Conduct quality inspections on the generated FR-4 sheet, including tests on electrical performance, mechanical performance, corrosion resistance, etc., to ensure that the product quality meets the standards.
In the actual production process, the specific process flow may vary due to factors such as the manufacturer and product requirements.
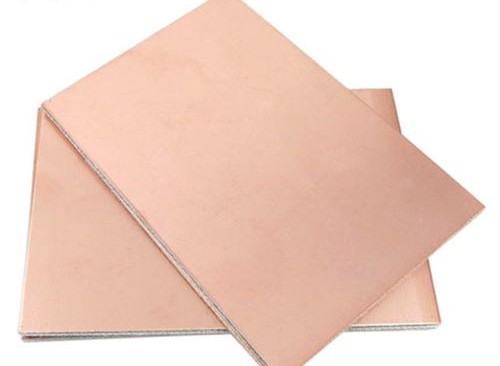
FR-4 sheet material is widely used in many fields due to its good performance, including but not limited to the following scenarios:
1. Electronic equipment: Such as the motherboards of computers, laptops, and tablets, as well as the circuit boards of mobile phones.
2. Communication field: Used in the manufacturing of circuit boards for communication equipment such as base station devices, routers, and switches.
3. Industrial control: Applied in the control circuit boards of industrial automation equipment and instrumentation.
4. Automotive electronics: The circuit boards of automotive electronic control systems, such as engine control units, braking systems, and in-vehicle entertainment systems, often use FR-4 sheet material.
5. Medical equipment: The circuit boards of various medical diagnostic equipment and treatment instruments.
6. Aerospace: Some electronic components of aerospace equipment also use FR-4 sheet material.
7. Consumer electronics: Such as the circuit boards inside televisions, audio equipment, and game consoles.
In conclusion, FR-4 sheet material plays an important role in modern electronic technology and provides a reliable basis for the stable operation of various electronic devices.
The common parameters of FR-4 sheet material include:
FR4 sheet parameter1. Glass transition temperature (Tg): Usually around 130 - 140 °C, which indicates that the physical properties of the sheet will change near this temperature.
FR4 sheet parameter2. Dielectric constant (Dk): Generally between 4.0 - 4.5. The dielectric constant affects the transmission speed and characteristics of signals in the sheet.
FR4 sheet parameter3. Loss factor (Df): Usually less than 0.02. A lower loss factor means less energy loss during signal transmission.
FR4 sheet parameter4. Moisture resistance: It has good moisture resistance and can maintain stable performance in a humid environment.
FR4 sheet parameter5. Bending strength: Reflects the ability of the sheet to resist bending deformation.
FR4 sheet parameter6. Coefficient of thermal expansion (CTE): Reflects the dimensional change of the sheet when the temperature changes.
FR4 sheet parameter7. Flame retardant grade: Generally reaches UL 94 V-0 grade, with good flame retardant performance.
These parameters may vary depending on the specific production process and manufacturer.
The following factors can affect the parameters of FR-4 sheet material:
1. Resin formulation: The composition and proportion of epoxy resin can significantly affect parameters such as the dielectric constant, glass transition temperature, and moisture resistance of the sheet.
2. Type and quality of glass fiber cloth: The weaving method, thickness, and material of the glass fiber cloth can affect parameters such as the mechanical strength and coefficient of thermal expansion of the sheet.
3. Production process: Including process parameters such as lamination pressure, temperature, and time. Insufficient pressure or uneven temperature may lead to inconsistent sheet performance; improper time control may affect the curing degree and thereby change the performance of the sheet.
4. Sheet thickness: Different thicknesses can affect parameters such as thermal conductivity and bending strength.
5. Environmental conditions: The temperature and humidity of the storage and usage environment can have an impact on the long-term performance of the sheet. For example, being in a high-temperature and high-humidity environment for a long time may reduce its insulation performance and mechanical strength.
6. Additives: The type and content of substances such as fillers and flame retardants added to the resin can change certain properties of the sheet, such as the flame retardant grade and dielectric properties.
The following are some factors that affect the dielectric constant of FR-4 sheet material:
1. Resin content and type: The content of epoxy resin and its specific type have a significant impact on the dielectric constant. Different resin formulations have different electrical characteristics.
2. Characteristics of the glass fiber cloth: Including the diameter, weaving method, and density of the fibers. These characteristics of the glass fiber cloth can change the electric field distribution inside the sheet, thereby affecting the dielectric constant.
3. Moisture absorption rate: After the FR-4 sheet absorbs moisture, the dielectric constant usually increases because water has a relatively high dielectric constant.
4. Operating frequency: At different frequencies, the dielectric constant of the FR-4 sheet may change.
5. Temperature: Changes in temperature can affect the arrangement and movement of molecules inside the sheet, thereby affecting the dielectric constant.
6. Manufacturing process of the sheet: Such as the degree of curing, lamination pressure, and time. These factors can affect the structural uniformity and compactness of the sheet, thereby affecting the dielectric performance.
7. Addition of fillers: The type, content, and distribution of inorganic fillers (such as silica, etc.) added during the sheet manufacturing process can change the dielectric constant of the sheet.